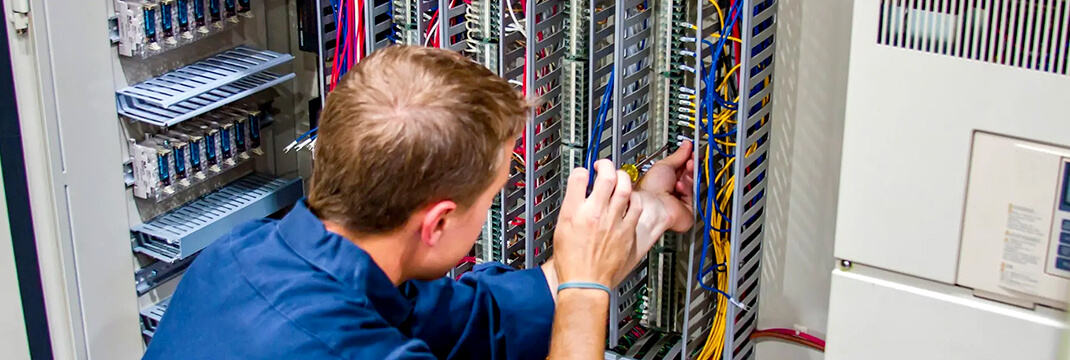
Hypothesis
How can a company improve quality assurance and control in Electromechanical Contracting and Maintenance? Does improving quality assurance and control in Electromechanical Contracting and Maintenance increase the company’s efficiency?
Executive summary
Quality assurance refers to the systems of ensuring that the right processes are followed in order to ensure the correct and effective operations of the company. Quality control, on the other hand, refers to the systems that ensure that the right products and of the right standard result from the production process. In the electromechanical industry, the right standard of production is inevitable in order to ensure consumer protection. The right standard of products can only be attained after the right procedures have been followed. This makes the two aspects inseparable in this industry, as well as in all other industries. Quality assurance and control are the two aspects that are of a great importance when it comes to the company’s efficiency. It is inevitable for the company to ensure that these two factors are running properly and functioning to aid each other. The use of the two will enable easy management. This project focuses on the two electromechanical companies, Topaz Energy and Marine and Cirta. These two have been very successful in the United Arabs Emirates in the electromechanical market. The two are also known for their use of quality control and assurance. The project seeks to understand how effective this has been, as well as the ways the two have managed to implement it. The project will also look on the challenges the two have met in the implementation of quality assurance and control. The research of this project will involve interviews with the managers of the research companies. This will help to come up with reliable information in this project. The research will also include wide reading on the topic. That is on how and why the companies should implement quality assurance and control. It will also involve reading on the ways these two aspects help to improve efficiency in a company. The research will also look on the ways that could be used to increase the efficiency of the two aspects. This will be elaborated in the conclusions and recommendations. Lastly, the paper will look at what companies that are not using these programs can do in order to have them working.
Introduction
In all industries, standard products are being advocated for. This is done in order to ensure that the consumers of these products are protected. The electromechanical industry is not an exception. Therefore, the standard of the products that result from the firms of this industry need to meet the set standards. This necessitates quality assurance and control. Quality assurance and control not only ensure the right quality of the product, but also employees’ safety. When the right procedures are followed in production, the number of possible accidents is minimized; therefore, the safety of the employees is ensured. It also means that the productivity of employees is increased. This ensures an overall increase in efficiency in the firm. Most firms have in place systems to implement this, but the systems are not up-to-date. Therefore, there is a need to improve these systems. This brings home the topic of this research. Improving quality assurance and control is a step that all companies need to take. To begin with, improved quality assurance and control increase the company’s efficiency and ensure its effectiveness. Hence, improvement of quality assurance and control will reduce the costs of production; thus, will increase the profit. This is because when the right procedures of production and quality assurance are followed, there is less waste and, thus, the costs become lower. In addition, when the right quality and standard of products are produced, more goods will be sold; thus, generating more sales. This means that there will be a high return and it will enhance wealth maximization. Hence, quality assurance and control work for the benefit of the company implementing it. The purpose of this paper is to evaluate the effectiveness of quality assurance and quality control in the two companies. The paper will compare the performance of the companies, while the companies are using effective quality assurance and control, and while they were using unimproved quality assurance and control. The intention of this comparison will be to weight the effectiveness of improving quality assurance and control.
Electromechanical Contracting and Maintenance
Improving quality assurance and productivity in business results in employee satisfaction and an increase in the number of the customer. Using quality administration system techniques, for example, benchmarking, process mapping, and cost-benefit analysis, it becomes possible to achieve a regular enhancement in all work-flow processes. Superior productivity leads to fewer defects, reduced costs, and fewer delays. Author, Fukada, came up with the following steps of improving productivity in order to achieve the objectives of the organization. Although these steps were originally Fukada’s idea, other authors have developed them further.
Step 1
Analyze the processes in the organization. Do not focus on the people carrying out certain tasks, but focus on the tasks they are carrying out. Standardize procedures and policies throughout the company in order to maximize competence and efficiency. Instruct all employees and personnel adequately in order for them to produce high-quality services and products, as well as to be proud of the work they do.
Step 2
Align the firm’s processes with those of other competing companies in that industry. The various tools, such as Process Clarity Framework, are provided by the Center of Quality and Productivity of America, in order to help to improve one’s business performance.
Step 3
During the performance measurements development you should benchmark your current processes. Then do problem identification and predict outcomes of the future measuring gains of productivity. This is done by using the key performance indicators of the industry. For instance, measuring productivity and quality in the customer supporting center will enable the company to know what are the customer expectations in order to improve on that ground. This is done by measuring time that it takes in resolving customer issues, as well as by counting the rate of customers’ satisfaction in the support cases.
Step 4
Building quality test into the processes should not be done at the end, when it is costly to fix. Measure the basic testing performance, then resolve the defective components problems without waiting the whole cycle to complete. Implement, if possible, an automated testing, since it executes minimum human intervention resulting in pass/fail outcome, which is simple to interpret, and the act upon it.
Step 5
Business strategies. Six Sigma, for example, should be used in improving the productivity and quality. Then create projects, which do problem definition, measure current processes, then gather the necessary data, analyze it to make valid the cause/effect relations. Determination of the main cause of that issue and designing proper intervention to improving or optimizing processes is a considerable step in improving quality assurance and control. Production should be controlled in order for the defects to be corrected early, before their impact influences the final product.
Step 6
Value the employees, suppliers, customers, and partners in the business; input and feedback regarding problem solving or products in service all steers towards improving quality assurance and control. Measure the productivity and quality gained through increases in satisfaction of customer. Then use feedback of customers in improving current products, as well as in influencing the design of the new ones. Averaging the requirements of the customers in the process of redesigning efforts can help in focusing your efforts on the highest lucrative places of businesses in the industry. For instance, conducting surveys and focusing on the groups to collect information to solve most of the issues with the product/service. Prepare the report, summarize and distribute it across your organization in order to improve productivity and quality. This helps in improving quality assurance and control.
Invite your friends and get bonus from each order they
have made!
Business Quality and Performance
According to Bessant and Francis, in order for the businesses producing goods or services to succeed, there should be a standard that is consistent. A number of recognized international systems is available to ensure that the achievement of quality is attained. The systems are helpful in increasing the efficiency in the process of production; moreover, it is an essential part in positive signals sending regarding the competitiveness of the product/service. These quality systems of assurance are vital in constructing a business reputation.
It is important to note that when you introduce a system of management to your business, you will be able to access a bigger market. The World Trade Organization, for instance, promotes specific management quality procedures through the best practice. Given the specific markets, such as the EU, as well as the US, have their own specific quantity and quality assurance standard in certain environment (such as production of food, for example), which supplement those standards of the World Trade Organization. Markets like the US and the EU have strict requirements regarding the international management quality standards.
This part will be explaining major internationally recognized quantity and quality standards of management, as well as the system going with them (Bessant, Francis, 2008).
According to Imai, improving the team performance of staff makes a lot of impact on the success of the business. Being the team manager, performance must be an important aspects, which is being constantly addressed in any business. Providing appropriate training in sales is a way of making sure that your staff is satisfied, so that the company can operate efficiently and the employees can work effectively (Imai, 1999).
Motivation
According to Magee, the staff performance must be maintained high through inspiration in order to make them have a higher driving force. They should work in liberty, enjoy their work, and feel passionate about it. The work must never be a chore; otherwise, the performance may suffer. It is important for managers to understand that the factors, which will give employees the determination to make an improvement in their jobs, in order for them to work as a team. A manager should motivate his/her employees through recognition of their performance in order to encourage them to develop. Motivating employees can be done by recognizing good performance and encouraging them to develop their skills. He/she should help them to develop their careers (Magee, 2006).
Appreciation
Magee continues to argue that this one may seem a minor thing; however, praising one for the job done well means more for the difference between a performing employee and a minimum output employee. Appreciation is necessary, even if it is verbal (Magee, 2006).
Working Environment
According to Williams and Fairbank, a wonderful working environment improves the employees’ productivity. Free communication of employees with one another and with the management, more so, when problems arise, is an effective tool of quality assurance and control. All the employees must be treated equally and with respect. The office politics generally tends to revolve around the same persons or groups of people, and so the employees are quickly addressed and made clear on the ways their negative behaviors may affect everybody (Williams, Fairbank, 2001).
Communication
Friedlander proposes that the employees should feel they free in approaching management anytime, whenever a problem arises. When there is an open door policy, employees should still feel appreciated. When a manager takes actions quickly in connection to their concerns, they feel happy and their performance improves (Friedlander, 2004).
Training
According to Armstrong, the employees, who are kept up-to-date with changes in the industry by being given the opportunity to train in both the area of specialization and also to gain skills for their own benefit, usually are motivated and succeed in their duties performance. This will make them feel that their own welfare is being looked upon. They will feel appreciated and will move together as a team. This definitely will enhance a positive change in the team performance (Armstrong, 2008).
Struggling with your essay?
Ask professionals to help you!
Start Chat
Encouragement
Durand and Eccles in their article argue that sharing of ideas amongst the employees should be encouraged. In meetings, there should be freedom of expression, meaning that meetings are not meant for executives. All employees should be included in the meetings and allowed to express their ideas on the ways they think the organization should be run. Normally, employees are specialized in the different areas, and so this calls the management to listen to what they have to say regarding their areas. Teams feel more motivated and encouraged, when they are given an opportunity to state their views on the ways of improving the efficiency and profitability of the organization. Berger (2000) explains that one should recognize the employees’ ideas mostly in meetings, ensuring that they receive credits. One needs also to recognize employees for their ideas, preferably in meetings, and to ensure that they receive credit (Durand, Eccles, 2007).
Reasons for Choosing These Two Companies
The decision to take under the research process and this project “CIRTA Electromechanical Contracting and Maintenance” is because it is Emirates-based company (local owner, founded and supported by Khalifa Fund) located in Abu Dhabi and Fujairah. Abu Dhabi’s branch exists since 2006, and until now it is very successful in the field of Electronic and Mechanical Contracting Works, same as in trading in Underground polycarbonate Manhole. Topaz Energy and Marine, on the other hand, is also the well-to-do company in the industry. The two are examples of success in the electromechanical industry. This is what prompted my research interest in them.