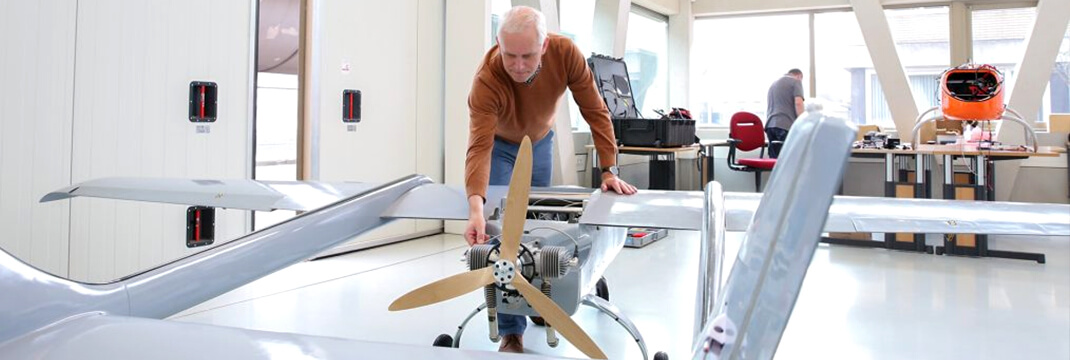
The number of air passengers and air cargo has rocketed in the new century thanks to constant improvement of the air transport vessels by aeronautical engineers as well as other professionals in the aviation industries. Air travel is arguably the fastest, safest and the most efficient means of transport. Airplanes exhibit different efficiencies depending on the nature of the system that powers the engines. The greater the electrification of the dependent systems of the airplane is, the higher the efficiency with regard to fuel consumption is (Sinnett, 2007). Therefore, there rises the need to replace the manual system with electrified ones thus reducing the fuel loss that will lead to increased efficiency. The engine of Boeing 787 is superior in many aspects concerning efficiency as compared to other engine systems of its predecessor planes due to its highly electrified systems. The manual system that has been replaced with the electrified ones in Boeing 787 and has significantly improved efficiency include the bleed-air system, the engine system, the hydraulic system and the electric system. Hence, efficiency of the system has increased, while operation and monitoring of the health status of the system simplified. Consequently, this decreased fuel consumption as a result of improved efficiency has promoted the reduced use of fossil fuels, which is a major concern to environmentalists. By attaining their aim of developing all-electric planes with electric powered engines, aeronautical engineers may develop a plane of maximum efficiency.
The Efficiency of the System
The Need to Develop Electric Engines
The need to increase electrification of the plane systems lies in numerous motivations based on the reduction of fuel consumption. To start with, environmentalists have raised the alarm on environmental pollution due to fumes released by fossil-fuel-propelled jet engines. Most fuels powering aircraft engines are kerosene-based. Pure kerosene is often mixed with some additives to prevent the kerosene from freezing under low temperatures when the plane ascends to high altitudes. Similarly, these additives protect the engine turbines of the planes from corrosion. The additives may include hydrocarbons, antioxidants and metal deactivators among others. Due to the threats posed to the protective ozone layer through corrosions by hydrocarbons, it is essential to decrease consumption of fossil fuel by the systems. Secondly, aviation industries, as well as other motor propulsion industries, may not be reliant on fossil fuels to power engines for too long. Oil is overexploited and will soon be depleted on the earth surface. Thus, oil prices have been gradually rising (Moir & Seabridge, 2012). Moreover, this brings the need to ensure reduced oil consumption through an increase in efficiency of systems. In its turn, electrification of the systems lowers fossil fuel consumption.
The aviation industry is looking forward to absolute usage of electric motors and fuel cells to fully drive the engines and eliminate the application of fossil fuel in totality. System efficiency of electric jet engines is involved in the conversion of stored energy to propulsion power in the jet engines. During each of these steps, energy is lost; hence, efficiency is reduced. The battery system has simpler conversion steps and averaged energy dissipation of 70%. Most of the battery energy is lost on the charging-recharging system to a tune of 50%. Nonetheless, this is incomparable to the kerosene driven engine such as Turboprop that has 40% efficiency and Turbofan, which has 30% efficiency. The main problem, however, relies on physics of the quantity of energy production by the electric motors. Batteries have an extremely lower energy density as compared to jet fuels (Hepperle, 2012). Therefore, electric powered planes can travel at a short distance before they deplete the power supply as compared to jets with engines powered by fossil fuels
Along with the first order offer - 15% discount (code firstpaper15), you save an extra 10% since we provide 300 words/page instead of 275 words/page.
Power Generators in Electric Aircraft
The electrical system in an aircraft consists of four main parts: power generator, the primary and the secondary power distributor, which also have the power protection responsibility, power converter, and storage. Power may be generated in either DC or AC form. The aircraft DC generators, on the other hand, are shunt–wounds that the armature is connected to the high resistance field coils in parallel. A commutator device is used to smoothen the generated DC to a simple sin wave output manner. AC generators do not require the commutator, and thus are simpler in construction. The AC systems used in airplane generators are the three-phase system in a 120° out of phase but connected to a neutral point. Hence, this layout makes the AC system produce a voltage of 115VAC as compared to the 28VCD produced by DC generators. Furthermore, this high voltage related to low current saves weight, since the conductors of the current are reduced in amount and weight as well. Besides, this is an advantage since weight reduction is a fundamental consideration in aircraft engine systems. Strides are being taken to ensure improved power output and decreased mass of the electricity supplier capable of the application on the airplanes.
Boeing 787
Boeing 787 is a United States plane constructed by the Boeing Commercial Airplane to replace Boeing 767. With a long-haul wide body and twin-engine system, Boeing 787 has almost 20% fuel efficiency as compared to Boeing 767, its predecessor. Having a greater electrified system, Boeing 787 has low noise and is environmentally friendly. Its materialistic blend consisting of 50% composite makes the Boeing a lighter plane (Baker & Monney, 2014). However, the wings are extensively made of aluminum while the windows made of electrochromism-based smart glass are larger than any other passenger plane, allowing the passengers to adjust illumination levels and enjoy the horizon view.
Boeing 787 has the greatest fuel efficiency owing to the high electrified system it contains. Boeing 787 has numerous variants with varying characteristics. They include the 787-8, which was the first aircraft to be commercially produced in 2011 with distance coverage of 13,621 miles. The 787-9, which had approximately 50% similarity with the 787-8 was a bit lengthened with a passenger capacity of 280. Boeing 787-10 stretched to match the passenger capacity of Airbus A350-900, i.e. over 300 passengers.
You may find this article Aviation Papers and Capstones Online Writers
useful.
Differences in System Architecture Compared to Former Aircraft Generations
Engine System
Boeing 787 is fitted by a twin-engine having a bleedless system due to the extensive electrification. The anti-ice system is the only remaining bleeding system in Boeing 787. The elimination of the pneumatic system has similarly reduced the complexity associated with both the mechanical and architectural design of Boieng 787. The reduced overall airplane power need can also be attributed to the elimination of the pneumatic system. The engine of Boeing 787, commonly known as the GEnx-1b Trent 1000 has numerous superior characteristic compared to other engine system including GE CF6-80C2 RR RB211-524G/H engines of 767 engines. The table below shows a comparison of properties of the two engines.
Table 1: Comparison of the characteristic of GEnx-1B, the Boeing 787 engine and Rolls-Royce Trent 1000 of Boeing 767. (Clark, 2012)
787 Engine( GEnx-1B Trent 1000) | 767 Engines: GE CF6-80C2 RR RB211-524G/H | |
Bypass Ratio | -10 | -5 |
Thrust Class | 53000-74000lbf | 53000-63000lbf |
Fan Diameter | 111-112 in | 86-93 in |
Specific Fuel Consumption | ICAO chapter 4 | ICAO Chapter 3 |
Emissions | CAEP/8(2014) | CAEP/2 |
Boeing 787 engines have a bypass ratio, the ratio between the mass flow rate of air in the bypass stream and the mass flow rate entering the core, of -10 while the 767 engines, on the other hand, has a bypass ratio of -5. The high bypass ratio lowers the Thrust Specific Fuel Consumption (TSFC) by almost 15% thus increasing the system efficiency (Dabkankich & Peters, 2017).
Secondly, the pressure ratio, the ratio between the absolute outlet and absolute inlet pressure, of GEnx-1B is 50 while that of GECF6-80C2 is 33. Thirdly, the thrust class of GEnx-1b extends from 53,000lbf to 74,000 lbf while that of GECF6-80C2 extends from 53,000 to 63,000 lbf. The fan diameter of the GEnx-1B engine is 111 inches while that of the GECF6-80C2 engine is 90 inches. The noise level of GEnx-1B is ICAO-chapter 4 while that of ICAO is Chapter 3. Finally, the emission of the GEnx-1B engine is CAEP/8 while that of GE CF6-80C2 is CAEP/2 (Clark, 2012). The following figure shows a model system of the GEnx-1B engine.
Bleed Air System
The engine bleed air system comprises the parts responsible for delivering and regulating the engine bleed air originating from the main engine or other power units to the components downstream. The main elements of the bleed air system include hydraulic reservoir pressurizer, engine start, engine cool ice remover and cabin air conditioning (Moir & Seabridge, 2012). The digital electronic control is used to regulate bleed air extraction as well as to minimize fuel burn.
Key
HX-Heat exchanger
XFR- Trans/rectifier
SG- Starter Generator
RAT-Ram Air Turbine
P- Hydraulic Pump
M-Motor
CTAI- Cowl Thermal Anti-ice
The bleed air system of Boeing 787 is electrical and it increases the fuel efficiency of the system. The incorporation of the engine generator and the starter functions to a single unit and the use of electrical power having variable frequency varies the constant speed drive hence reducing the architectural and mechanical complexity of the generator. Besides the role of engine generator as the starter motor, these changes have enhanced the elimination of pneumatic starter from the engine. Overall, the changes have increased the mean time between faults to 30,000 flight hours, a 300% improvement in reliability as compared to the bleed air system of Boeing 767. Other benefits accrued by the electrical system include the elimination of energy loss of the pre-coolers, simplification of the auxiliary power unit and the elimination of the bleed air losses through the compression stages of the discrete engines. Therefore, the efficiency of the engine has increased by 15% by contrast to the actual engines.
Hydraulic System
The operation of the landing gear through the flight deck display is performed through the hydraulic system. Other operations done by the hydraulic gear embrace the brakes as well as the flight control surfaces. A simple hydraulic system used in small aircrafts consists of 5 main parts: the pumps dissipate pressure to the whole system, which is the power generating device, the reservoir is the storage vessel of the hydraulic fluid, the actuating cylinder is the central organ of the hydraulic system, the pressure relief valve controls the pressure in the hydraulic system and the heat exchanger maintains the hydraulic fluid as shown by figure 3 below. The hydraulic fluid contains three types of fluid, namely the mineral-based fluid, polyalphaolefins or the phosphate esters.
Boeing 787 incorporates three separate hydraulic systems each having 5000 psi. The wing spoiler and their engine thrust reversers are powered by the right and the left system controls. On the other hand, the center system powers the landing gear actuation, flaps, nose-gear steering and the slats. However, the flight controls are powered by both the right, the left and the central systems (Norris, 2012). The twin electric motor driven pump that powers the center system is the main distinguishing feature of the hydraulic system in Boeing 787 differentiating it from other hydraulic systems. The center system of the predecessor engines is powered by two huge air-turbines operating at 3000 psi to ensure that the peak hydraulic demands are met to allow landing gear actuation and lift actuation. Hence, this portrays one of the noticeable prime differences between the engine system of Boeing 787 and the traditional engine system that lies in the power source of the center system.
A significant electric improvement was made in the hydraulic system of Boeing 787 from the hydraulically actuated brakes in Boeing 767. The move eliminated the possibility of delays due to leaking hydraulic fluids from the valves and other hydraulic failures. Since the electric brakes system is independent on the four wheels, the 787 is capable of dispatching with a single electric brake actuator (EBA). Although the EBA is line-replaceable, in-situ maintenance is possible. Consequently, this makes monitoring of the brakes system for their health status as compared to their hydraulic or pneumatic system.
Invite your friends and get bonus from each order they
have made!
Electrical System
The electrification of all the systems in Boeing 787 makes it a superior plane with regard to fuel consumption and efficiency. With the installation of the three-phase 230VAC electric power, Boeing 787 is uniquely electrified by contrast to other systems having the common 115 VAC arrangements. It is fitted with an electric system, which is regarded a hybrid of 235VAC, the 115 VAC, the 28VDC and the 270 VDC (Moir & Seabridge, 2012). Therefore, wiring of the system is reduced in Boeing 787 due to decreased current flow as a result of the increase in voltage dissipation by a factor of 2. The environmental control system consumes electric energy to remove the bleed air through the application of pressure. Thus, this consumes approximately 500kVA. The wing anti-icing responsible for availing the bleed air, on the other hand, requires 100Kva while the four independent electric motor pumps that replace the hydraulic system need approximately 400Kva of power.
Summary and the Next Generation of All Electric Aircrafts
Improved electrification of the system leads to the increased efficiency and reduced amount of fossil fuels in the aviation industry. Future developments of aircrafts may be based on absolute electrifying of the planes including equipping them with electric engines. With reduced battery size and increasing power output and storage or the advancement of the electric motor and the fuel-cell physics, the field of aeronautical engineering is targeting to fit airbuses by electrical system in the coming two decades. However, fuel cells have been the prime target of energy generation in the next generation planes. With water as the main waste of fuel cell combustion during energy production, the effect of aviation industry on the environmental degradation as well as noise pollution will be greatly mitigated.
Conclusion
The skyrocketing of air transport has led to the necessity of improving the efficiency of the air vessels thus, reducing fuel usage, which has a major impact on the environment. The aviation industry needs to enhance the efficiency of planes by adopting a more electric system. Improved electrification of the four main systems, in particular the engine system, the hydraulic system, the bleed air system and the electric system in Boeing 787 as compared to its predecessor planes has been proved to increase the overall system efficiency thus decreasing fuel consumption. Lower fuel consumption reduces the environmental degradation. Boeing 787, unlike its predecessors, Boeing 777 and Boing 767, has a highly electrified system that ensures simplicity in operation as well as monitoring making it a more powerful plane. The all-electrification of the system, which may predictably be achieved by 2030, will have a very high efficiency and negligible environmental influence.